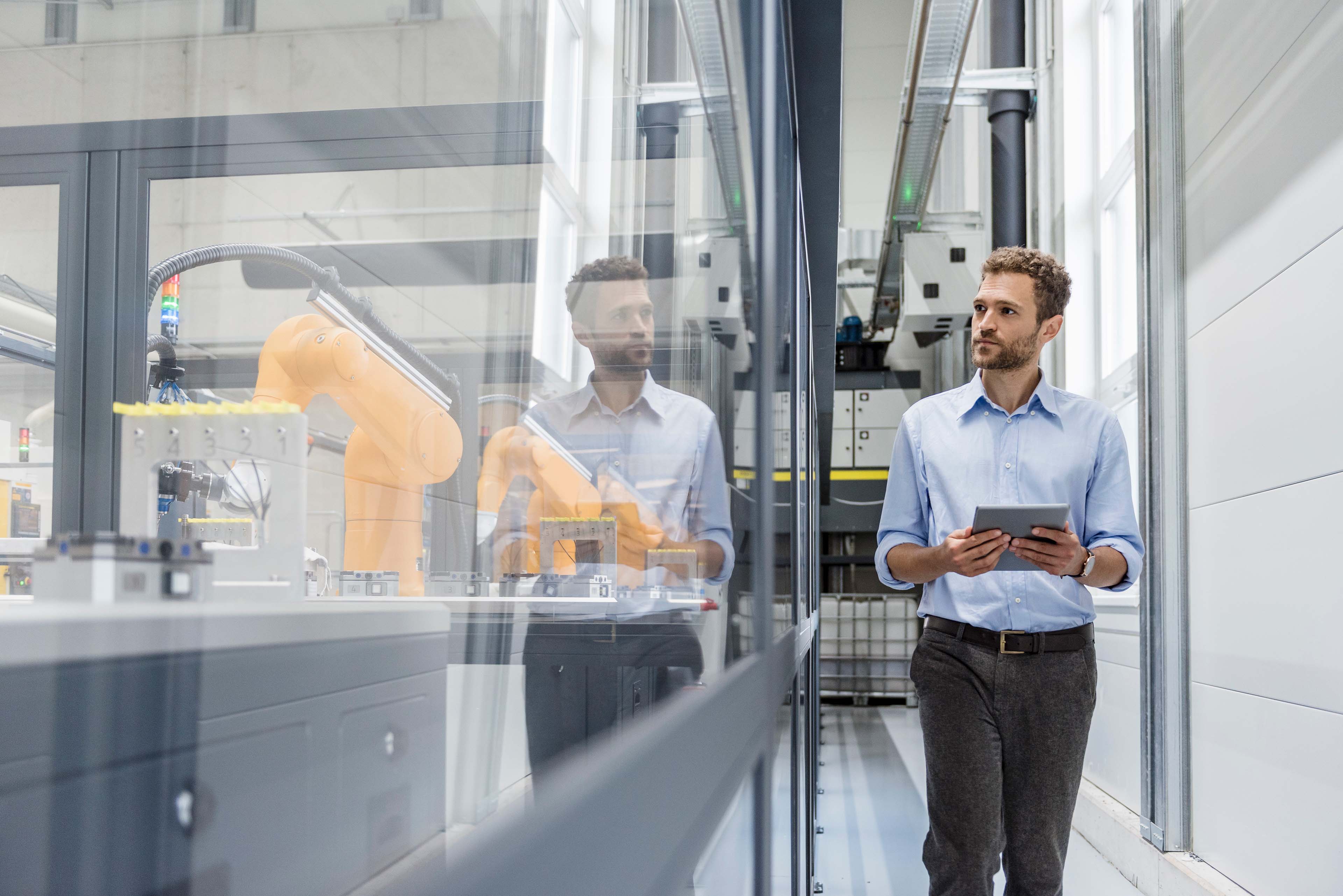
Production Part Approval Process
Elekta uses a single global PPAP process for approving new or changed parts
Production parts are approved using Elekta's 'PPAP process'. This process is used for new parts, modified parts by engineering change to prove that the changes to the manufacturing process or supply chain are controlled and can ensure that a capable manufacturing process is in place that can meet Elekta's customer and quality requirements. We have an 18 element PPAP process to follow although not all elements are used for every part or change. Your assigned SDQ Engineer will discuss in advance which PPAP elements are required for your part or change, taking into consideration product complexity and risk. Once agreed, Elekta then expects the PPAP evidence to be sent to Elekta for the SDQ Engineer to review and accept before parts are cleared for shipment into Elekta.